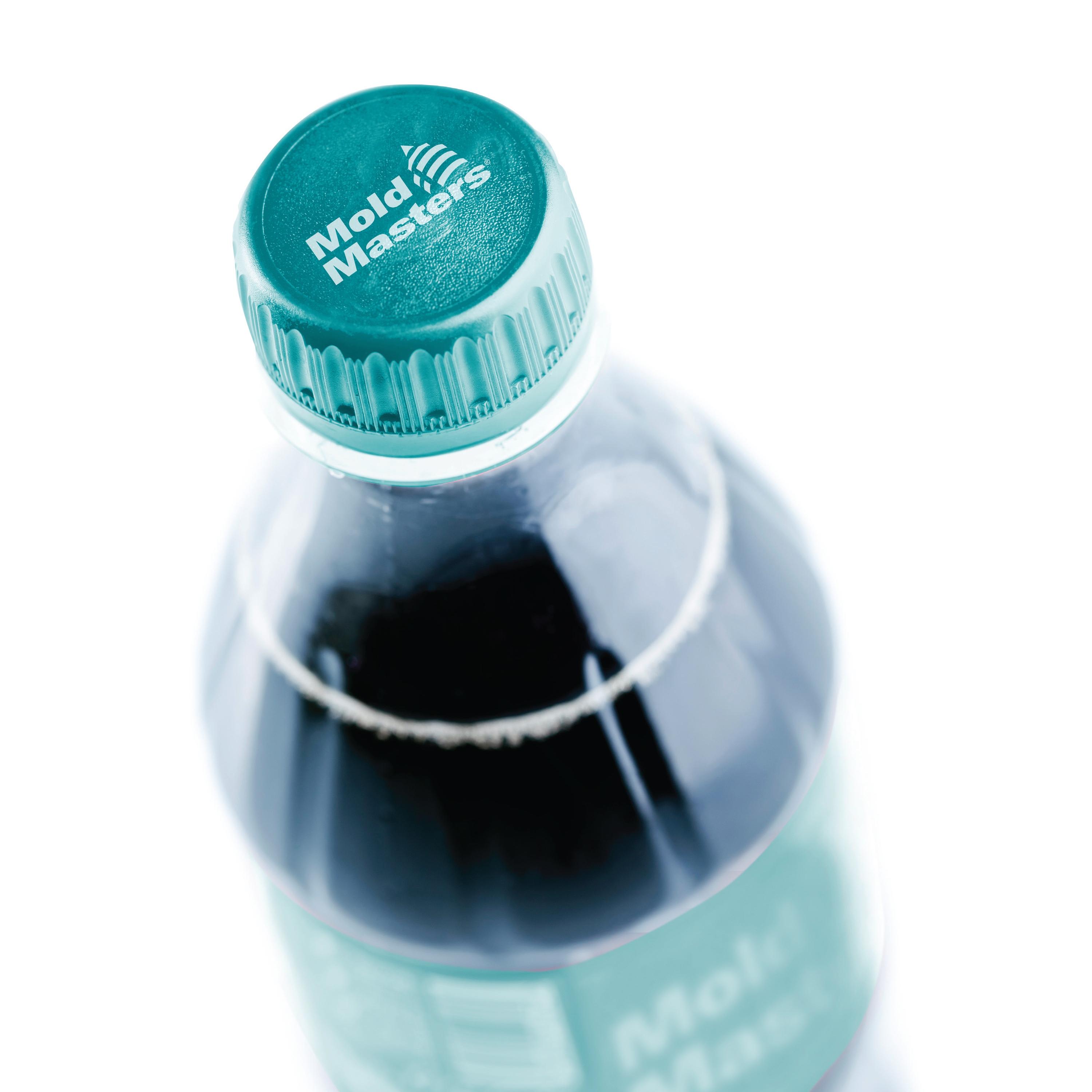
CAPS & CLOSURES
Mold-Masters® New Sprint Apex Gate Seal Gaining Marketplace Traction
Mold-Masters recently introduced its new innovative premium Sprint APEX gate seal, designed to serve as the new standard for cap and closure molds. It offers customers processing and maintenance advantages that significantly improve part quality and lower operating costs. The new seal has already been adopted by several molders, who have seen multiple improvements to overall product quality and cost effectiveness.
The Sprint APEX gate seal improves environmental stress crack resistance (ESCR) on CSD caps by up to 40% which supports sustainability by enabling the potential for light weighting and the use of recycled and bio-based resins that may not have the same ESCR durability as conventional resins.
Additional improvements include appearance quality on caps that have difficulty hiding flow lines; better color change performance (up to 65%) compared with standard gate seals; and the elimination of vespel insulation caps, a wear item, for reduced maintenance costs.
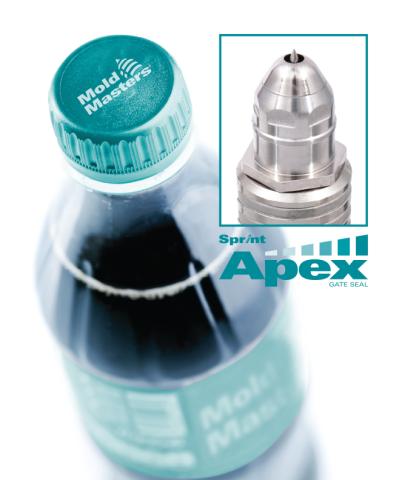
CUSTOMER EXAMPLES
ENVIRONMENTAL STRESS CRACK RESISTANCE (ESCR)
A major beverage molder has designated APEX to become its new standard gate seal after various performance test results.
During testing, which included multiple dimple designs, the molder compared APEX to a traditional 3 and 6-hole gate seal tip design in the production of 1881 CSD caps. Customer test results showed stress crack failures occurred on caps molded with the traditional gate seal design.
Alternatively, APEX eliminated stress cracking on all dimple and non-dimple designs. The beverage molder has already retrofitted existing molds and will incorporate APEX as the new standard in any new hot runner systems.
IMPROVING APPEARANCE QUALITY
Mold-Masters Sprint APEX gate seal significantly minimizes flow lines. This processing benefit also improves the appearance quality of caps that have difficulty hiding flow lines. While colorant has a major impact on flow line appearance, APEX improves cap appearance quality regardless of colorant used. Applications include transparent decorative caps, shampoo caps, detergent caps, and more.
Example A: Purple Flip-Top Cap
In the first application, a major closure molder experienced a cloudy appearance on the top of the cap after a resin/colorant change which could not be processed away. After conversion to APEX, the clouding effect was eliminated without process adjustments.
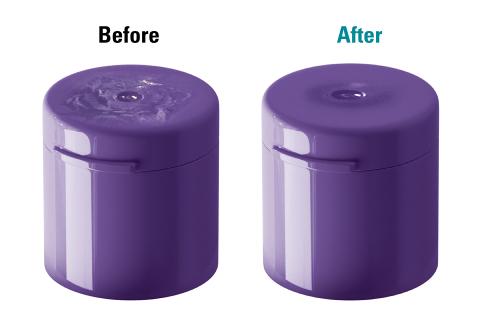
Example B: Satin Cap
In the second application, a major cosmetic molder experienced flow lines on the top of a large detergent cap produced in a natural and satin finish. A switch to APEX significantly minimized flow lines, making them no longer visible. Additionally, APEX accommodated a gate detail that matched the customer’s standardized cavity interface.
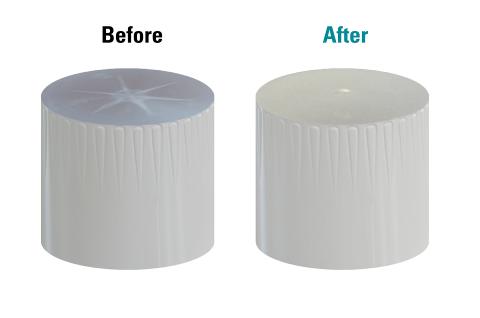
FASTER COLOR CHANGES. MINIMIZING SCRAP.
APEX also provides scrap reduction and helps sustainability initiatives by enhancing color change performance. A customer reported that one color change on a competitors hot runner design produces approximately 30,000 closures (60kg) of scrap using their standard gate seal tip. With Sprint APEX they were able to speed up the color change process and reduce their color change scrap by about 50% (15,000 closures - 30 kg).
REDUCTION OF MAINTENANCE COSTS
APEX gate seals have also eliminated vespel insulation caps, a wear component common with traditional industry-standard gate seal designs. Generally, these vespel caps get frequently replaced as part of regular maintenance. On a high-cavitation hot runner system the annual cost of these spare parts alone is about $10,000 per mold (not accounting for labor/downtime). APEX benefits molders enormously by reducing the ongoing maintenance costs for production companies.
EASILY UPGRADE YOUR EXISTING SYSTEMS
The new Sprint APEX Gate Seal is compatible with the Mold-Masters Sprint Hot Runner system as it features industry-standard cut-out and sealing dimensions that make it interchangeable with a standard hot-tip gate. Additionally, existing molds using competitive hot-runner systems can be retrofitted with a Sprint Hot Runner system that incorporates Sprint APEX Gate Seals. When retrofitting, customers can reuse their existing cavity inserts, making the conversion process more economical and shortening ROI.
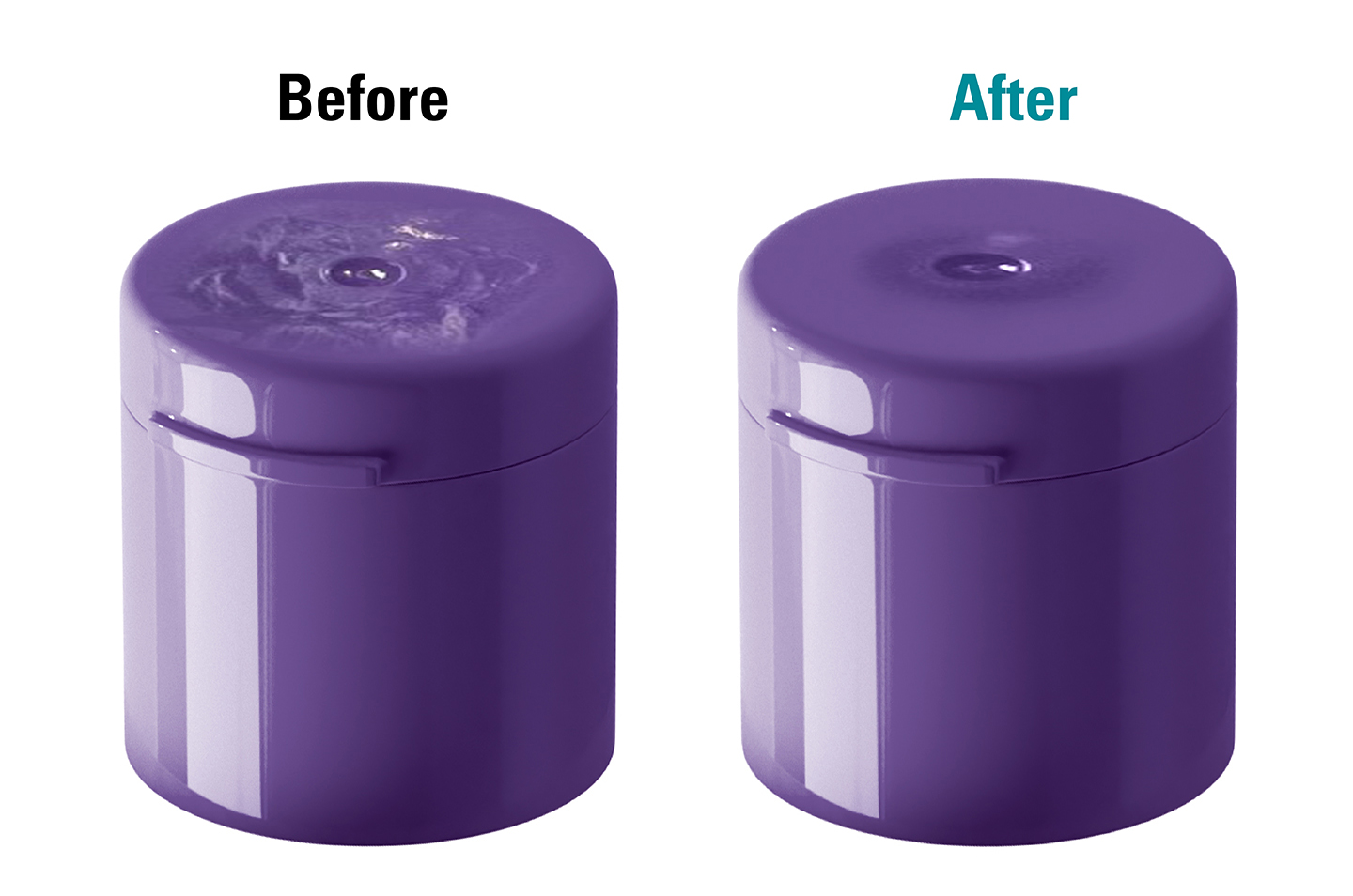
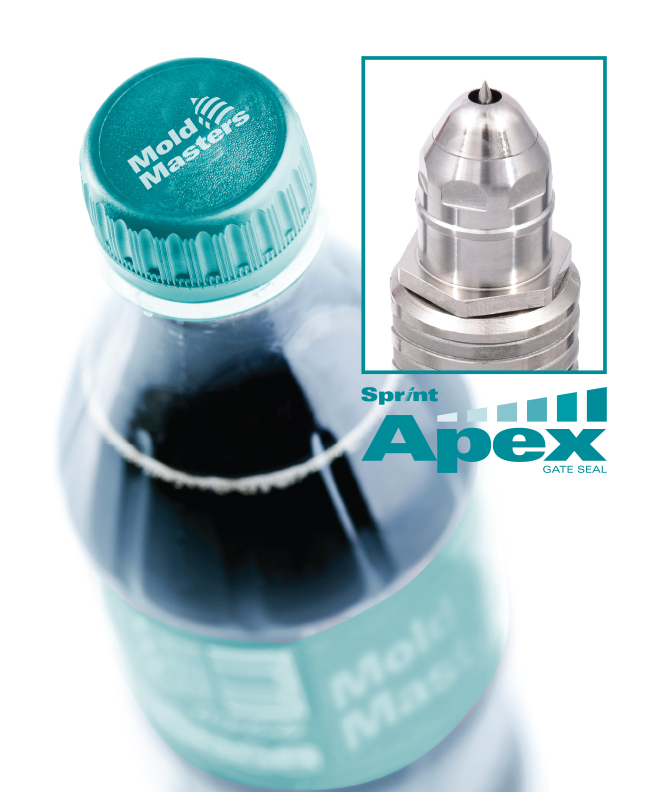
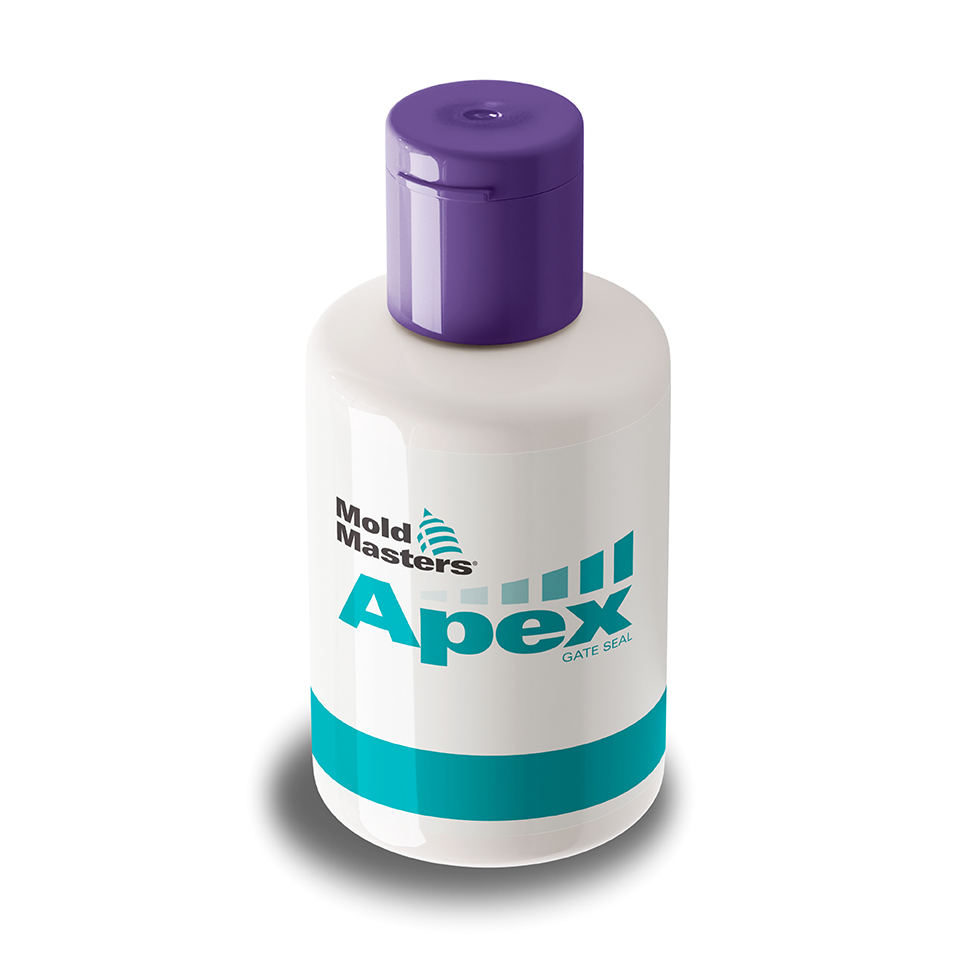
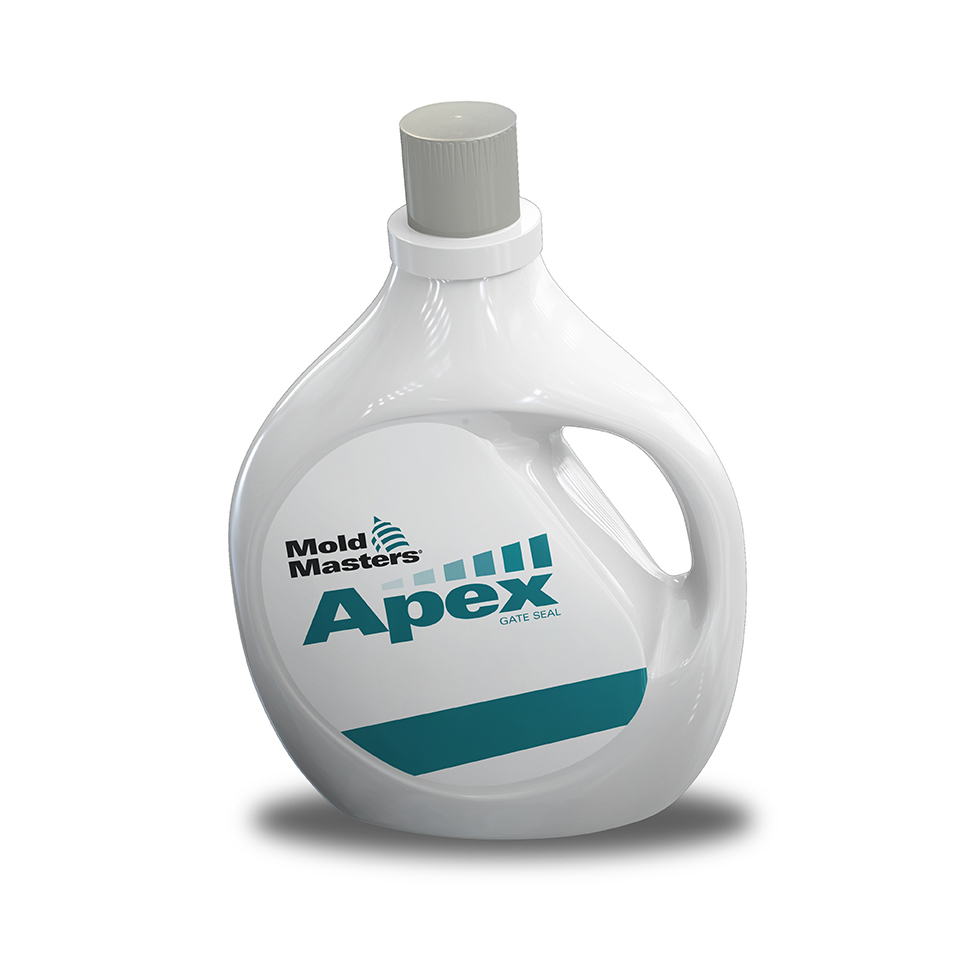