Mold-Masters认识到我们在您为实现可持续发展目标而做出的努力中所发挥的重要作用。这通常涉及将现有产品的材料转换为更可持续性的替代方案。我们在生物树脂应用知识、经验和成功方面处于行业领先地位。因此,我们是您处理可持续生物树脂和回收利用(PCR)应用的最佳合作伙伴。我们现有的许多解决方案都非常适合处理可持续发展材料。当您准备好了,我们也已准备就绪。
Common Resins
Case Studies
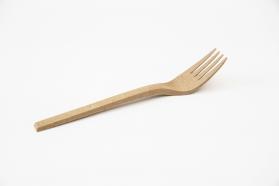
生物树脂一次性餐具
对我们而言,马斯特不仅仅是一个供应商,更是我们的研发合作伙伴。
- Josef Žádník, CEO, Refork
通过使用独家配方的生物树脂混合材料,Refork公司利用注塑模具生产可持续使用的一次性餐具。生物树脂材料由木粉(主要材料来自木材行业的边角料)、PHA(粘合剂)和各种可再生矿物质(用于增强机械性能)组成。这种特殊的混合材料在家庭堆肥、土壤或海洋环境中可以完全地进行生物降解。Refork餐具包括一系列叉子、刀子和勺子。网址: www.refork.com
Refork在早期阶段就与马斯特展开合作,开发出适合注塑成型的专用混合材料。该过程包括对各种生物聚合物(如PLA、PBAT、PHA)进行测试,验证他们作为粘合剂的作用。为了保证最终产品取得成功,需要实现几个关键变量,包括以下几点:
- 高标准的生物降解性
- 具备良好的机械性能
- 适用于食品接触
- 具有良好的可加工性
- 外观吸引人(颜色/质地)
- 适合大规模生产
- 较高的热变形温度(HDT)点
在注塑工艺中,Refork要求马斯特克服以下三个关键挑战:
- 防止材料降解(这种生物树脂材料由于生物聚合物粘合剂和木粉的影响,在注塑过程中往往会迅速发生降解)。
- 当产品进行大规模生产,可以实现一致循环时间。
- 尽量减小注塑压力,可以使系统兼容较小的设备。
马斯特根据每种产品所需的生产能力,提供了多套经过优化的马斯特热流道系统(热半模)。其中包括48和24点热半模,以及用于研发测试的4点热半模。此外,马斯特的TempMaster M2+热流道温度控制器也被用以保持严格的工艺控制。
马斯特与Refork密切合作,提供热流道解决方案,使其成功实现了所有目标。Refork不仅能够加工他们独特的材料,而且马斯特的热流道能够保证一致的循环时间,减少废料,并将所需的注塑压力减小了500bar,从而使模具能够在较小的机器上运行。目前,Refork每月使用马斯特的热流道生产超过1200万个生物树脂餐具(年产1.51亿个)。
如果您有可持续的生物树脂或PCR应用,请联系我们获得解决方案。