经济实惠的大批量生产、完美的质量、难以成型的聚合物和紧迫的交期是汽车行业面临的挑战,因为它希望制造更轻的零件,以提高燃油经济性,同时支持准时制(JIT)的交货要求。常见应用包括汽车外饰、汽车内饰、发动机罩下部件和汽车车灯(照明)。
Requirements
Common Resins
MM Solutions
Case Studies
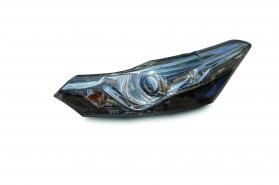
前车灯透镜
SEVG+(伺服电动阀浇口)可实现TIER 1照明应用的快速优化处理。
马斯特的某家客户是一家一级(TIER 1)汽车照明零件制造商,该制造商与北美某个著名品牌签订了合同,生产一款新型电动SUV的前车灯零件。由于电动汽车不再需要气流进入发动机舱,是所以这种新型的PC照明组件可以横跨整个前格栅。
对于汽车品牌方来说,他们最为关注的是生产出来的零件表面上没有任何可见的流痕迹。根据我们的模流分析,进行连贯地填充才能获得必要的结果。然而,该制造商一贯使用的气动阀不能提供实现该零件持续生产所需的可重复性或准确性。
马斯特用于该应用的热流道解决方案是Fusion G2系统(F7000喷嘴、延长阀浇口), 并结合了我们先进的SeVG+(伺服电动阀浇口)驱动控制系统。SeVG+系统因其简单紧凑的设计以及马斯特的销售和工程支持而受到客户的青睐。SeVG+采用直接驱动设计,不同于包含操纵杆、齿轮箱和其他零件的其他品牌同类系统。这不仅减少了备件需求,而且最大限度地减少了开框需求。此外,我们新的第二代电机的高度降低了48%,最大限度地降低了堆叠高度。该电机的高度现在只有90毫米高。
在这个特殊的应用中,热流道系统的每个喷嘴/浇口都连接一个子流道,并将融熔料导入到零件的左侧和右侧。共有3个子流道。
起初,外侧的两个浇口(1号和3号)存在散状流痕的问题。为了消除这一问题,马斯特通过对这些浇口进行分段处理来解决。阀针在行程的前50%缓慢打开,然后剩下行程中迅速打开。对每个浇口进行单独处理,使得这一问题得以在不到10次射料中迅速解决。
如果这个热流道系统没有配备SeVG+系统,解决散状流痕 需要调整注塑工艺,这将会影响所有的浇口,包括正常运行的中心浇口。很明显,在具有挑战性应用中,SeVG+系统能够精确控制单个浇口的运行,这种灵活性使得工艺解决方案变得高效且简便。

双色注塑(2K)侧视镜
提供稳定的加工过程、最低的废品率和快速的ROI(投资回报率)。
“我完全相信这是目前市场上符合我们加工需求的最好的辅助注塑单元。”
马斯特的客户为诸如菲亚特、阿尔法罗密欧、Lancia、IVECO、大众、福特、斯柯达、宝马等品牌设计和制造汽车后视镜。该类应用一开始使用另一个品牌(以下简称品牌A)的液压辅助注塑单元来生产新款双色注塑(2K)汽车侧镜。
历经数个月,该款双色注塑(2K)汽车零件的工艺都无法得到稳定,导致了各种零件缺陷,包括毛刺和短浇料,废品率约为14%。客户的目标是通过优化工艺和更新设备,恢复高效率、低成本的生产。此外,由于他们当时使用的品牌A的辅助注塑单元有特殊的维护要求,所以与类似设备相比,该品牌的单元停机时间也显著较高。
客户尝试选择 Mold-Masters 的 E-Multi 辅助注塑单元(EM3-100-28)来替换表现不佳的品牌A的辅助注塑单元。
E-Multi 安装在现有的注塑机上,采用水平配置,并提供了客户当前使用的品牌A注塑单元所不具备的其他功能(例如:高达10个可编程注塑配置,带有保压压力)。E-Multi 的全面概括性能、统计工艺数据功能以及全方位生产跟踪为进一步改善以前系统中不可访问的参数提供了新的了解渠道。
在配置该生产单元时,虽然系统集成并非首要任务,但在作为整体过程管理的“大脑”、消除多余设备、省宝贵的厂房空间这三个方面,E-Multi 控制系统体现出了巨大的优势。E-Multi 控制辅助注塑成型过程,整合了温度控制和其他各种智能控制功能成为一体化控制设备。
在安装 E-Multi 并进行工艺优化后,该项目使用E-Multi生产的废品率减少到低于1%。在不到4个月的时间内,客户节省了15,000欧元,并且系统在不到2年内完成摊销(原计划生产6年以上)。由于 E-Multi 极低的维护要求,生产过程的停机时间也显著减少。
我们的客户意识到,购买使用其他品牌的最便宜的设备并不总能帮助他们的业务获取最大利益,因为性能和质量对他们的运营至关重要。E-Multi 证明了一件事,选择使用*总拥有成本(TCO)很低的设备,能够使投资迅速得到回报。E-Multi 还可以为工程和车间团队节省大量麻烦。*总拥有成本(TCO):Total Cost of Ownership,包括产品采购、后期使用、维护的成本。
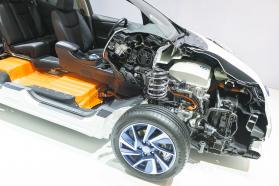
锂离子电池盖
在挑战PFA电池应用方面,Summit系列将正常运行时间延长400%+
一家新顾客向我们咨询了有关模制锂离子电池盖的问题,以满足电动汽车行业对PFA树脂的日益增长的需求。这种特殊的树脂对锂离子电池盖应用非常重要,因为它可以抵抗电池液的腐蚀,并且可以防止电池过度充电。传统上,由这种材料制成的组件是用冷流道生产的。但是,由于材料非常昂贵,客户希望转用热流道以降低废料并减少生产成本。
PFA树脂的成型要求使任何注塑机都面临挑战。这种树脂的主要问题在于,在加热过程中,材料会释放出对钢具有腐蚀性的氟气。热流道系统和注塑机都受到这种气体的影响。一旦腐蚀开始,腐蚀就会迅速蔓延并导致阀针卡死并最终泄漏。在联系Mold-Masters之前,客户曾尝试与其他几家热流道供应商合作,但都以失败告终。他们的系统只能运行一周,然后需要大量维修和清理维护。这不是可持续的做法,因此客户继续寻求更好的解决方案。
这个难得的机会使Mold-Masters与客户紧密合作,以确保他们的成型应用成功。Mold-Masters Summit系列热流道系统特别适合此类应用,因为它旨在适应具有腐蚀性/磨蚀性或对温度/剪切敏感性的挑战性树脂。Summit系列将各种特殊材料和涂层结合到其组件中,以保护系统免受有害腐蚀性材料的影响,从而延长维修间隔。
与竞争对手相比,通过使用Mold-Masters Summit系列热流道,正常运行时间增加了至少400%(1个月vs. 1周)。 如果模具保持连续生产,则某些Summit-Series系统可以保持生产长达12周(100万次循环),从而大大延长了维修间隔和计划外停机之间的时间。 该客户对结果非常满意,现在依赖于Summit系列热流道系统来进行此应用的成型。
Mold-Masters Summit系列热流道系统通过PFA应用获得了了明显的竞争优势。这一成功必将使更多的制造商转向Summit系列的PFA应用,最终通过增加正常运行时间和减少废品来收回成本。