Mold-Masters recognizes the important role we play as part of your efforts towards your sustainability goals. This often involves converting materials of existing products to more sustainable alternatives. We lead the industry in Bio-Resin application knowledge, experience and success. As such, we are your best partner for processing sustainable Bio-Resin and post consumer recycled (PCR) applications. Many of our existing solutions are well suited to processing sustainable materials. We're ready when you are.
Requirements
Common Resins
MM Solutions
Case Studies
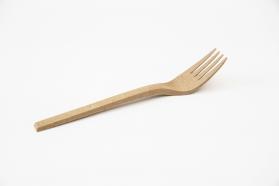
Bio-Resin Single Use Utensils
FOR US, MOLD-MASTERS IS MORE THAN A SUPPLIER, THEY ARE A DEVELOPMENT PARTNER
- Josef Žádník, CEO, Refork
Utilizing a proprietary Bio-Resin blend, the company Refork, utilizes injection molds to produce sustainable single use utensils. The Bio-Resin material consists of Wood Flour (primary material sourced as waste from the wood industry), PHA (binder) and various renewable minerals (to enhance mechanical properties). This special blend is fully biodegradable in home compost, soil or marine environments. Refork utensils include a selection of forks, knives and spoons. www.refork.com
Refork developed their proprietary blend that would be suitable for injection molding by involving Mold-Masters at an early stage. That process involved testing various biopolymers (PLA, PBAT, PHA’s) which would act as the binder. There were several key variables that needed to be achieved for the end product to be a success. This included:
- High biodegradability criteria
- have good mechanical properties,
- be acceptable for food contact,
- offer good processability,
- be visually appealing (color/texture),
- be suitable for mass production,
- higher HDT (Heat Deflection Temperature) point.
There were 3 key challenges during the injection molding process that Refork needed Mold-Masters to overcome:
- Prevent material degradation (The bio-resin material tended to degrade quickly during the injection process as a result of the biopolymer binders and wood flour).
- Achieve a consistent cycle time that could be scaled to mass production.
- Minimize the injection pressure to allow system compatibility on a smaller machine.
Mold-Masters supplied several optimized Master-Series hot runner systems (hot halves) depending on the production capacity that was required for each product. This included 48 and 24 drop production hot halves and a 4-drop hot half for R&D testing. Mold-Masters TempMaster M2+ hot runner temperature controllers were also utilized to maintain tight process control.
Mold-Masters worked closely with Refork to supply hot runner solutions that allowed them to successfully achieve all of their goals. Not only was Refork able to process their unique material, but Mold-Masters hot runners were able to achieve a consistent cycle time, minimize scrap and decrease the required injection pressure by 500 bars to allow the molds to be operated with smaller machines. Mold-Masters hot runners are currently used by Refork to produce over 12M Bio-Resin utensils on a monthly basis (151M annually).
If you have a sustainable Bio-Resin or PCR application contact us for an application review today.