Medical components are often complex, high-clarity transparent, low weight parts with tight tolerances that demand exceptional molded part quality. We represent your best choice for producing the highest quality part through our superior process control and repeatability. We were the first to successfully mold with many engineering grade resins such as PC, PBT, POM and COP. You can also rely on our global support network to support expansion into emerging markets. Common applications include medical devices, PPE, syringes, pipette tips, blood vials, pill bottles and more.
Requirements
- Highly technical components/applications
- Part weight range from <1g to 500g+ (typical)
- Excellent surface and gate quality finish
- High repeatability
- High productivity
- High reliability
- Clean room requirements
- Compact mold designs
- Ability to process thermally sensitive and corrosive resins
- Multi-material molding
- Extending shelf life and freshness.
Common Resins
MM Solutions
Case Studies
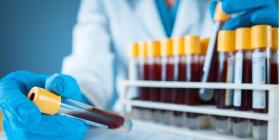
New SYMFILL Technology
SIGNIFICANTLY MINIMIZE BARREL BOW BY UP TO 90% (AS LOW AS 0.15mm).
Producing Medical Blood Tubes is a mature, high volume market, which is served by multiple ‘A’ brand hot runner suppliers. Generally, molds for this product range from 32-96 cavities. Mold-Masters has introduced a proven technology for this application that improves part quality tolerances (barrel bow) by up to 90%. Significant improvements beyond what the industry accepts as being possible within the current standard tolerance limits. Mold-Masters blood tube technology has the potential to be an industry game-changer.
Mold-Masters was challenged to find a technical solution that would minimize core deflection in the molding process of PET blood tubes. As a rule, long thin tubes require cores mounted in the injection mold to be able to produce the desired geometry. Difficulties arise when filling the cavity resulting in shear and thermal changes that affect the viscosity of the material impacting core shift resulting in barrel bow of the part due to wall thickness deviations. Generally, the industry widely accepts and understands that producing long thin-walled parts means tolerances will be demanding and next to impossible to attain during production times.
Due to the very aggressive L/T and very thin core of blood tubes, a barrel bow of 0.5-1.5mm is commonly accepted amongst all molders, toolmakers and HR suppliers involved in this market segment. Mold-Masters has achieved barrel bow as little as 0.15mm (70-90% improvement). Benefits from improved part quality include:
- Tubes roll concentrically in the labelling machine.
- Increases final stage throughput.
- Minimizes machine downtime.
While the industry has learned to deal with the results related to certain core deflection, this new solution opens a huge window of opportunities for light weighting, cycle time savings, reduced scrap, etc.
This puts Mold-Masters a unique position to provide results that no other hot runner suppliers can match. That’s “Performance Delivered”.
For more information contact us today: https://www.moldmasters.com/form/contact-us